Troubleshooting Your Equipment: When to Call for Packaging Machine Repair
Troubleshooting Your Equipment: When to Call for Packaging Machine Repair
Blog Article
Quick and Reliable Packaging Equipment Fixing Provider to Reduce Downtime
In the competitive landscape of production, the efficiency of product packaging operations pivots on the integrity of machinery. Quick and reputable repair work solutions are crucial in minimizing downtime, which can lead to significant monetary losses and operational troubles.
Relevance of Timely Repairs
Timely fixings of product packaging machines are crucial for keeping functional performance and reducing downtime. In the fast-paced atmosphere of manufacturing and packaging, also minor breakdowns can result in considerable hold-ups and productivity losses. Addressing issues without delay ensures that equipments operate at their optimal ability, therefore securing the circulation of operations.
Additionally, timely and regular upkeep can avoid the rise of minor problems right into significant breakdowns, which commonly incur higher repair work prices and longer downtimes. An aggressive technique to equipment repair not just protects the integrity of the tools yet also boosts the general integrity of the assembly line.
Furthermore, prompt fixings add to the longevity of packaging equipment. Makers that are serviced quickly are less likely to deal with too much wear and tear, permitting organizations to maximize their investments. This is especially important in industries where high-speed packaging is vital, as the demand for constant efficiency is paramount.
Advantages of Reliable Company
Reliable company play a pivotal function in making certain the smooth procedure of product packaging makers. Their experience not only boosts the effectiveness of fixings however additionally adds significantly to the longevity of tools. Reputable solution suppliers are geared up with the technological knowledge and experience necessary to detect issues accurately and apply efficient solutions promptly. This reduces the threat of persisting troubles and guarantees that machines run at optimal efficiency degrees.
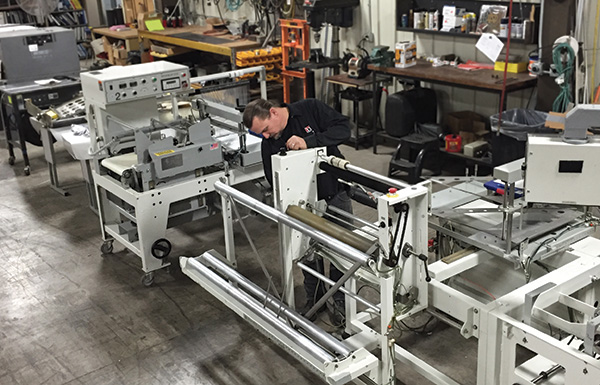
In addition, a respectable service provider supplies extensive support, consisting of training and support for team on equipment procedure and upkeep ideal techniques. This not just empowers workers however also grows a society of security and efficiency within the organization. Overall, the advantages of involving trustworthy provider prolong past instant repair services, favorably influencing the whole operational workflow of product packaging processes.
Typical Packaging Maker Problems
In the realm of packaging operations, various concerns can jeopardize the efficiency and functionality of equipments (packaging machine repair). An additional typical concern is imbalance, which can cause jams and unequal product packaging, influencing item top quality and throughput.
Electric issues can likewise interrupt product packaging operations. Damaged circuitry or malfunctioning sensors might lead to unpredictable machine behavior, causing delays and boosted functional costs. In addition, software application glitches can impede the equipment's programs, leading to functional ineffectiveness.
Inconsistent item flow is another crucial issue. This can occur from variations in item shape, weight, or dimension, which might influence the machine's ability to take care of things pop over to this site accurately. Inadequate training of drivers can intensify these problems, as untrained employees might not acknowledge very early indications of breakdown or might abuse the tools.
Resolving these typical product packaging device problems without delay is necessary to preserving productivity and guaranteeing a smooth operation. Routine evaluations and aggressive upkeep can dramatically alleviate these problems, cultivating a dependable product packaging environment.
Tips for Minimizing Downtime
To reduce downtime in packaging operations, applying an aggressive maintenance technique is critical. Regularly scheduled maintenance checks can identify potential problems prior to they escalate, making sure devices operate effectively. Establishing a routine that consists of lubrication, calibration, and evaluation of critical components can considerably reduce the frequency of unanticipated breakdowns.
Educating staff to run machinery appropriately and identify very early indication of malfunction can likewise play a crucial role. Equipping drivers with the understanding to do fundamental troubleshooting can avoid minor concerns from creating major delays. Furthermore, keeping a well-organized stock of important spare parts can accelerate repairs, as waiting for components can lead to prolonged downtime.
Furthermore, documenting device efficiency and upkeep activities can help identify patterns and reoccurring problems, allowing for targeted treatments. Integrating innovative surveillance innovations can give real-time information, allowing predictive upkeep and reducing the danger of unexpected failings.
Last but not least, promoting open interaction between operators and upkeep teams makes certain that any kind of irregularities are immediately reported and attended to. By taking these aggressive procedures, businesses can boost operational performance and considerably reduce downtime in product packaging procedures.
Selecting the Right Repair Work Solution
Selecting the ideal repair work solution for packaging equipments is a critical decision that can considerably impact functional effectiveness. Begin by evaluating the supplier's experience with your certain kind of product packaging equipment.
Next, think about the solution provider's credibility. Seeking responses from various other organizations within your sector can supply insights into integrity and quality. Qualifications and partnerships with identified equipment manufacturers can additionally show a commitment to excellence.
Additionally, assess their feedback time and schedule. A provider who can provide prompt support minimizes downtime and keeps production circulation consistent. It's also crucial to ask concerning warranty and service guarantees, which can reflect the confidence the service provider has in their work.
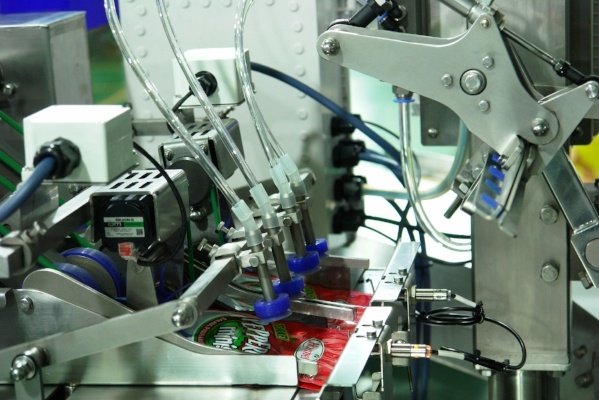
Final Thought
Finally, the relevance of fast and trusted product packaging equipment repair work solutions can not be overstated, as they play an important function in decreasing downtime and guaranteeing operational efficiency. By Click This Link prioritizing timely repair work and selecting trustworthy company, businesses can properly attend to typical concerns and preserve performance. Implementing aggressive upkeep techniques and buying personnel training more improves the long life of product packaging machinery. Inevitably, a strategic approach to repair services promotes an extra durable production setting.
Prompt repairs of packaging makers are crucial for maintaining operational efficiency and minimizing downtime.In addition, prompt repair work add to the durability of packaging equipment. Generally, the advantages of engaging trusted solution providers extend past immediate repair services, favorably influencing the whole operational operations of product packaging procedures.

Report this page